Nuclear Services
SOCOTEC’s engineering and technical staff have provided support and engineering services to both US and international nuclear plants for nearly sixty years. Our experts have been called upon to investigate component failures, provide engineering support for component improvement, and to demonstrate system operability. Depending on specific needs, clients typically collaborate with us through one of our service offerings or directly based on the areas of specialization and expertise of our staff.
Component Operation Simulation
SOCOTEC can develop component operation simulation using a combination of modeling, kinematics and analysis to simulate performance under operating scenarios. SOCOTEC's experience has encompassed various air-operated valve and check valve behavior, simulation sequencing of spent nuclear fuel loading into casks, and construction load sequencing.
We have capabilities to test component performance through data acquisition and digital capture.
Operability Assessments
The life expectancy of components is continually challenged with the aging of the nuclear fleet in the US. This often results in degraded conditions that require assessments to support continued plant operation. SOCOTEC’s engineers have evaluated many such components, often with tight schedules necessary to support determinations. We can quickly mobilize experts to work independently or with plant teams to develop the technical basis in support of plant operability determinations.
Nuclear Program Support Services
SOCOTEC has been actively involved in many of the most significant programs in the nuclear industry in the last 20 years. These have included FAC programs, valve programs, service water system fluid transients, buried piping and gas intrusion analysis services.
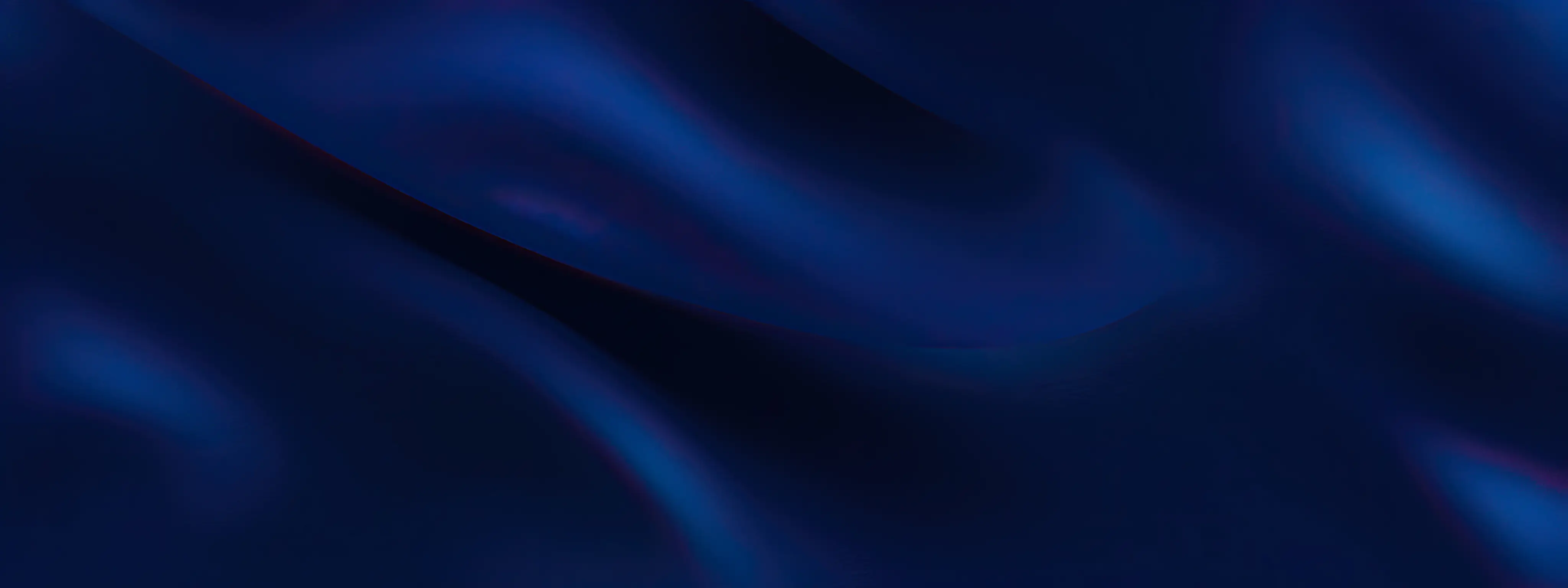
Talk to our experts
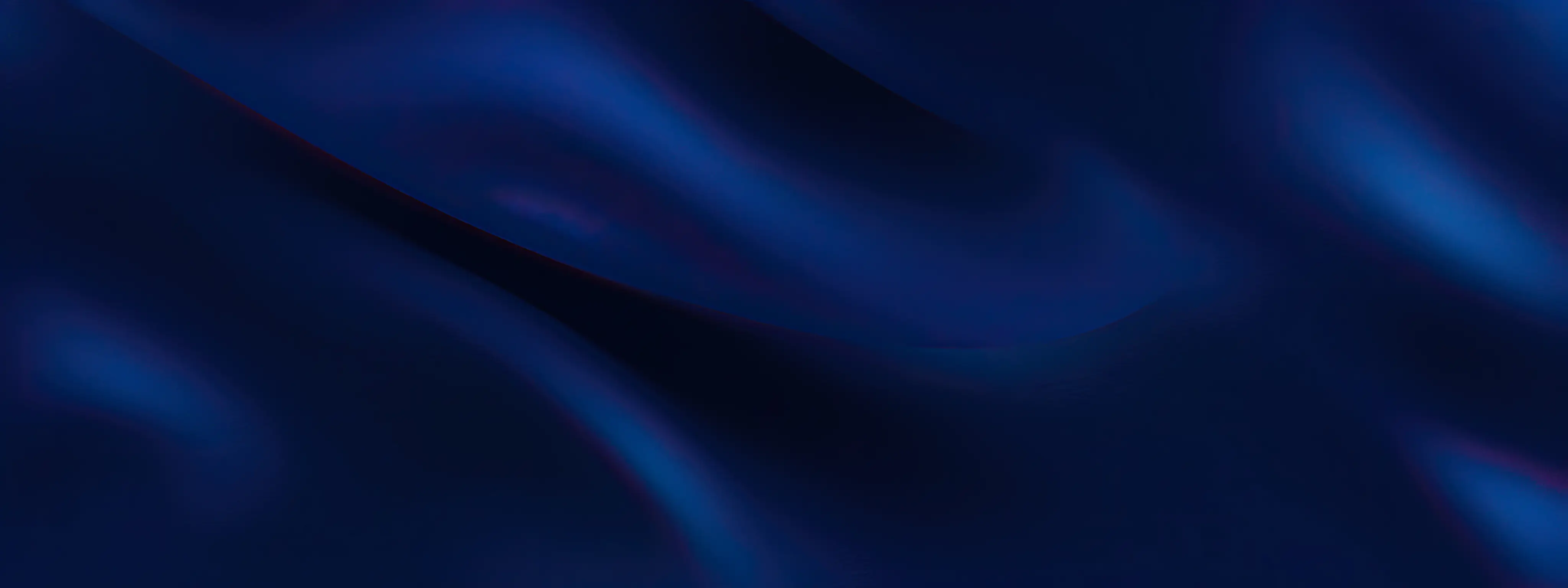
Nuclear Services
Flow Accelerated Corrosion (FAC)
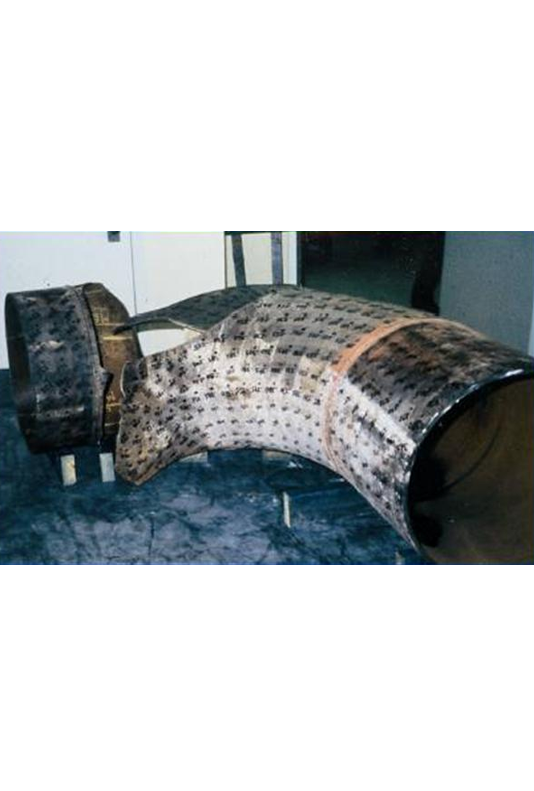
FAC can lead to wall thinning in pipes, valves heater shells, and tanks in BWR, PWR, and CANDU nuclear plants and within fossil power plant systems. FAC is the dissolution of the normally protective oxide layer on the inside surface of carbon and low alloy steel piping. The iron oxides that naturally form on the exposed surface of the pipe are removed by mass transfer to the de-oxygenated water flowing over the pipe's inside surface.
Resulting failures of pressure components can lead to catastrophic events, with significant downtime for repairs. SOCOTEC’s personnel have been involved in FAC assessments of piping systems since the early identification of this problem in US nuclear plants. Our experience extends to all nuclear power plant types, and the review of a significant number of fossil stations.
We understand how plants operate and work closely with plant personnel, soliciting input and valuable insights from system engineers, operations, maintenance, and NDE personnel.
FAC can lead to wall thinning in pipes, valves heater shells, and tanks in BWR, PWR, and CANDU nuclear plants and within fossil power plant systems. FAC is the dissolution of the normally protective oxide layer on the inside surface of carbon and low alloy steel piping. The iron oxides that naturally form on the exposed surface of the pipe are removed by mass transfer to the de-oxygenated water flowing over the pipe's inside surface.
Resulting failures of pressure components can lead to catastrophic events, with significant downtime for repairs. SOCOTEC’s personnel have been involved in FAC assessments of piping systems since the early identification of this problem in US nuclear plants. Our experience extends to all nuclear power plant types, and the review of a significant number of fossil stations.
We understand how plants operate and work closely with plant personnel, soliciting input and valuable insights from system engineers, operations, maintenance, and NDE personnel.
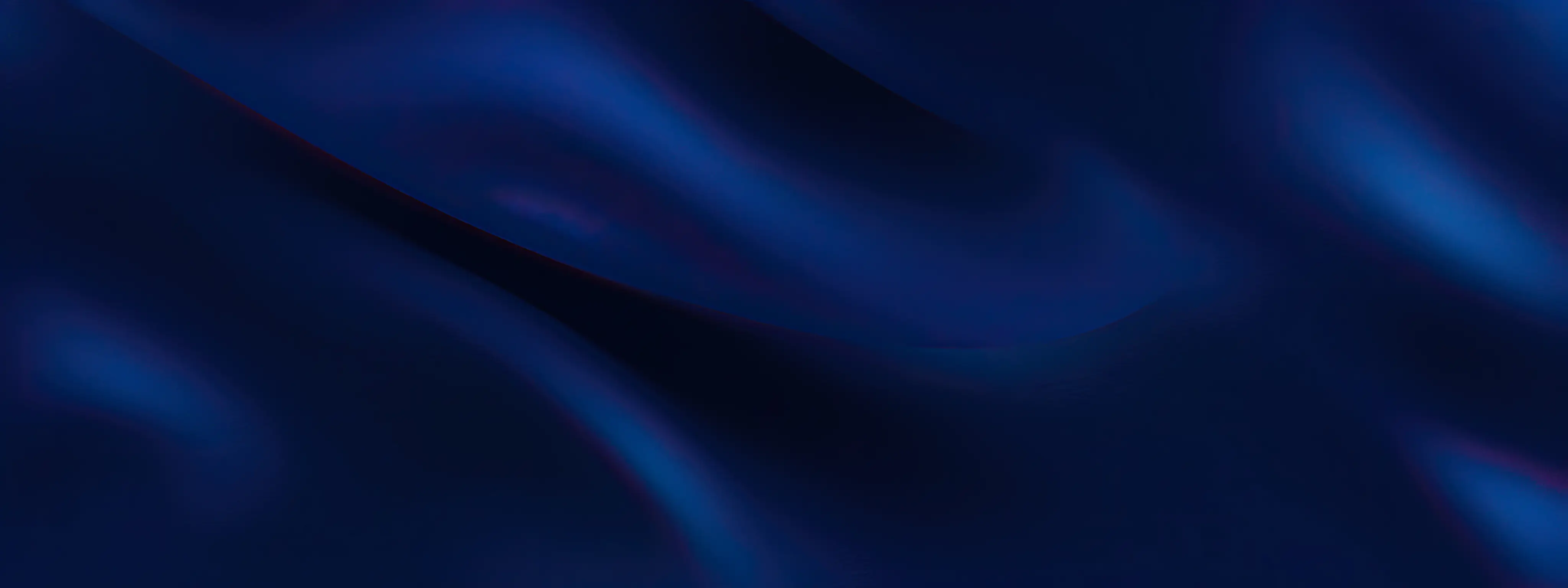
Nuclear Services
Valve Programs
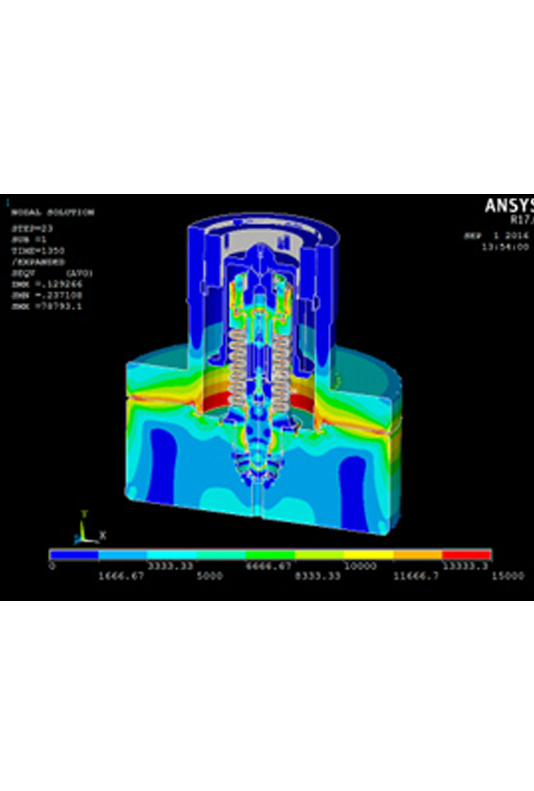
Our valve analysis experience extends over many years, with active involvement since the beginning of the GL89-10 motor-operated valve program in US nuclear plants. Our engineers have performed assessments using our structural engineering capabilities to develop weak link assessments, our mechanical engineering abilities to perform set-up and capability evaluations, and our fluid engineers predict flow, drag, blow-down, and check valve performance. SOCOTEC's capabilities and service encompass:
Valve failure analysis
Valve and actuator mechanical analysis
Qualification of valve designs to meet structural and performance specifications
Analysis to predict valve performance for motor-operated, air-operated, and hydraulically operated gate, butterfly, globe and check valves
Valve/actuator design modifications
Valve analysis per ASME code requirements
Our valve analysis experience extends over many years, with active involvement since the beginning of the GL89-10 motor-operated valve program in US nuclear plants. Our engineers have performed assessments using our structural engineering capabilities to develop weak link assessments, our mechanical engineering abilities to perform set-up and capability evaluations, and our fluid engineers predict flow, drag, blow-down, and check valve performance. SOCOTEC's capabilities and service encompass:
Valve failure analysis
Valve and actuator mechanical analysis
Qualification of valve designs to meet structural and performance specifications
Analysis to predict valve performance for motor-operated, air-operated, and hydraulically operated gate, butterfly, globe and check valves
Valve/actuator design modifications
Valve analysis per ASME code requirements
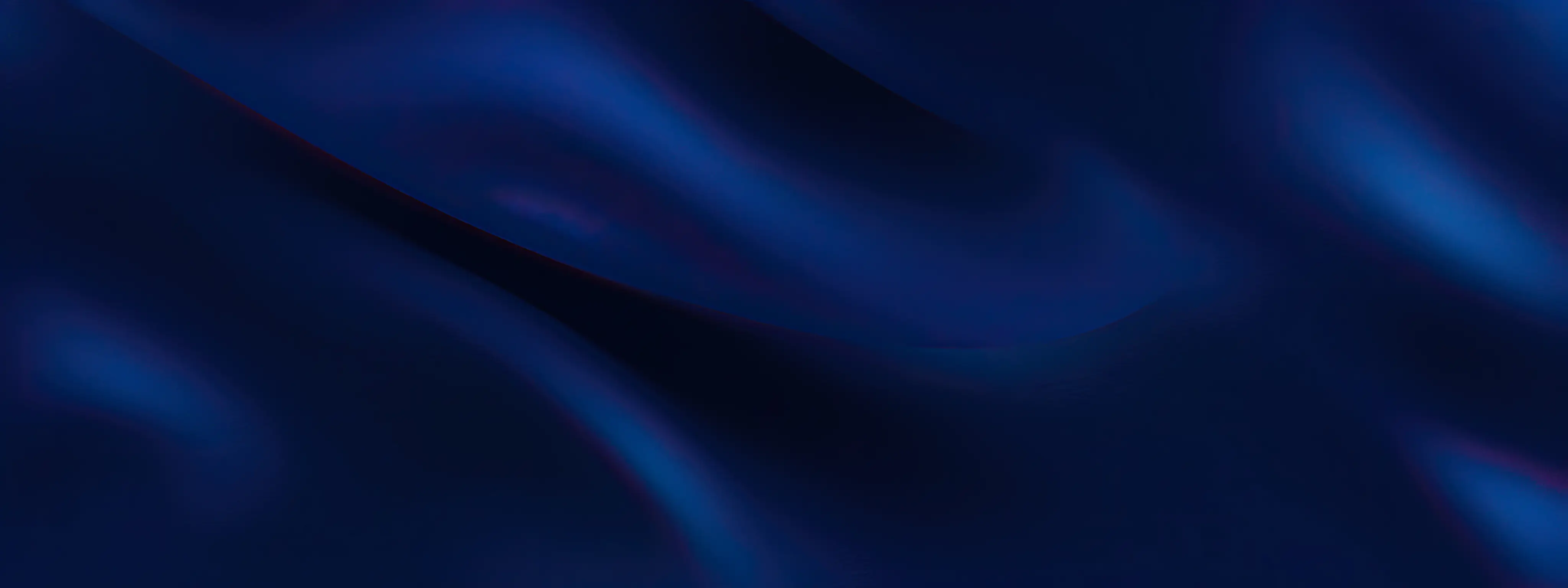
Nuclear Services
Buried Piping Programs
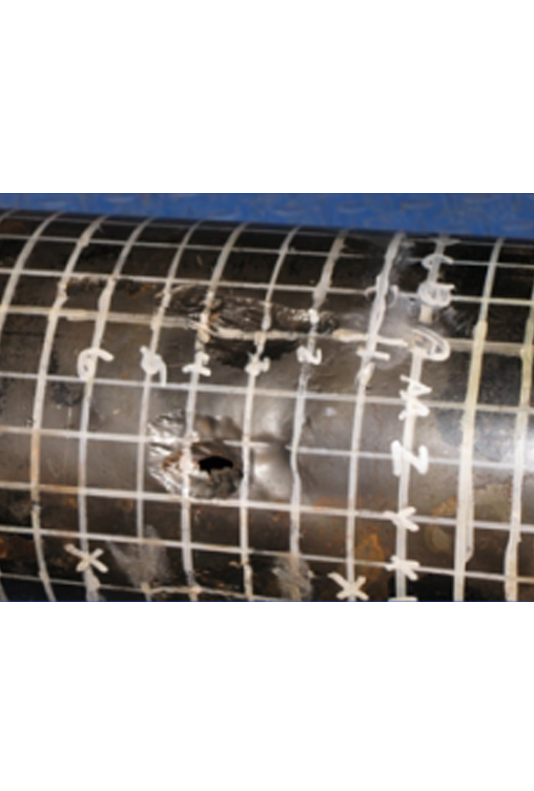
Degradation of buried piping is a major issue facing nuclear power plant owners, and many plants will require repair or replacement of existing carbon steel piping components. Although degradation mechanisms are often slow, they are progressive. As plants reach 30 and 40 years of operation, increased instances of inadvertent radiological release from these underground systems are expected, based on the industry experience to date. This has been an issue for license renewal, and plants have generally been required to commit to opportunistic inspections of these underground systems.
Many nuclear plant systems contain one or more lines that are buried. These systems may include safety and non-safety service water, circulating water, fire protection, diesel fuel oil, spent-fuel pool cooling water, miscellaneous radioactive lines, off-gas, and yard drains. Many buried lines are coated or tape-wrapped with materials such as concrete, coal tar, asphalt-based materials, or epoxy. Although many of these lines were cathodically protected when plants were constructed, in many cases the cathodic protection system may not have been maintained or used consistently. The result is accelerated external degradation at locations where the coating has failed. Additionally, certain systems can be subject to internal corrosion as a result of microbiologically influenced corrosion (MIC), and other degradation mechanisms.
Degradation of buried piping is a major issue facing nuclear power plant owners, and many plants will require repair or replacement of existing carbon steel piping components. Although degradation mechanisms are often slow, they are progressive. As plants reach 30 and 40 years of operation, increased instances of inadvertent radiological release from these underground systems are expected, based on the industry experience to date. This has been an issue for license renewal, and plants have generally been required to commit to opportunistic inspections of these underground systems.
Many nuclear plant systems contain one or more lines that are buried. These systems may include safety and non-safety service water, circulating water, fire protection, diesel fuel oil, spent-fuel pool cooling water, miscellaneous radioactive lines, off-gas, and yard drains. Many buried lines are coated or tape-wrapped with materials such as concrete, coal tar, asphalt-based materials, or epoxy. Although many of these lines were cathodically protected when plants were constructed, in many cases the cathodic protection system may not have been maintained or used consistently. The result is accelerated external degradation at locations where the coating has failed. Additionally, certain systems can be subject to internal corrosion as a result of microbiologically influenced corrosion (MIC), and other degradation mechanisms.
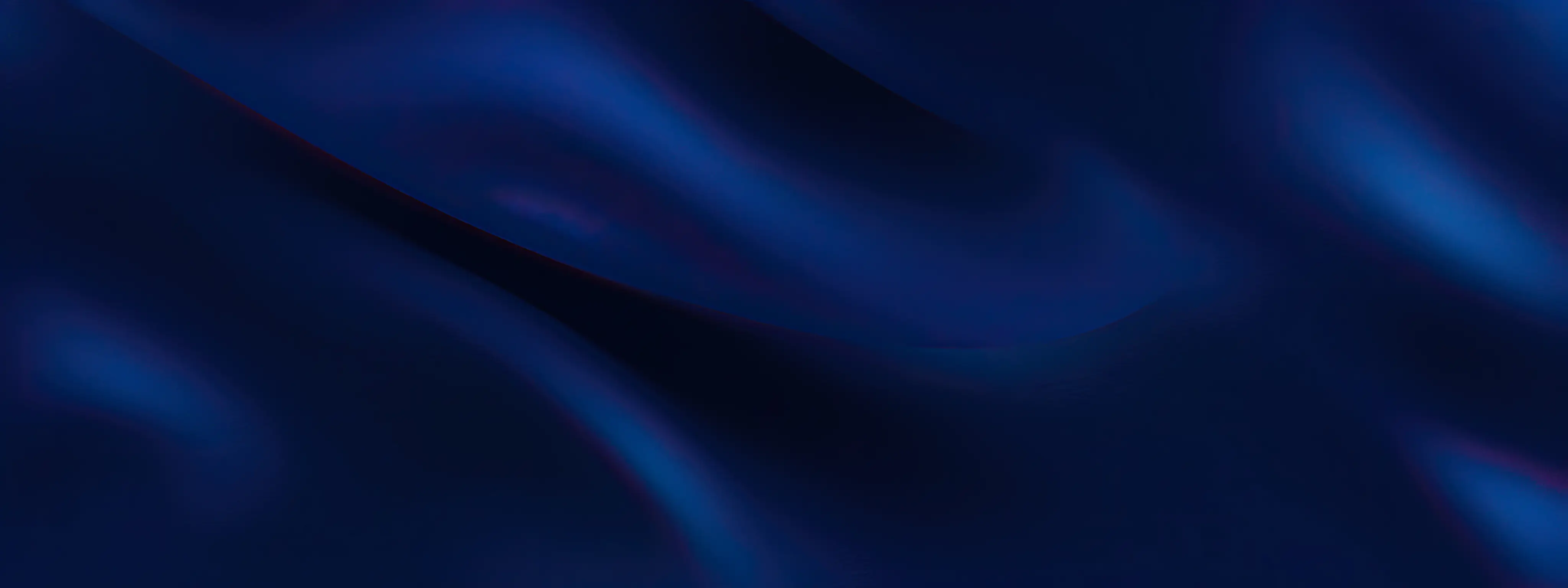
Nuclear Services
SOCOTEC Value
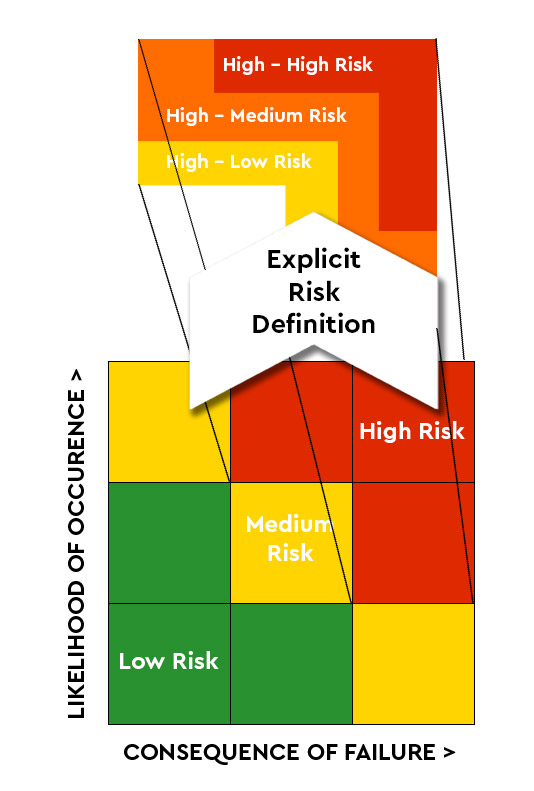
SOCOTEC can offer our clients the expertise of our staff with extensive experience in corrosion control, program development, and fitness-for-service assessments. Our experience encompasses program development services, including risk ranking, NDE planning, direct examination, and data evaluation, based on our comprehensive Fitness-for-Service expertise.
Our experience includes:
Fleet support services for a leading US operator
Model and database development
Risk ranking of fleet SSCs (including radiological piping, tanks and sumps)
Drawing development for ease of location of plant SSCs and monitoring wells
SOCOTEC can offer our clients the expertise of our staff with extensive experience in corrosion control, program development, and fitness-for-service assessments. Our experience encompasses program development services, including risk ranking, NDE planning, direct examination, and data evaluation, based on our comprehensive Fitness-for-Service expertise.
Our experience includes:
Fleet support services for a leading US operator
Model and database development
Risk ranking of fleet SSCs (including radiological piping, tanks and sumps)
Drawing development for ease of location of plant SSCs and monitoring wells
Nuclear System and Component Aging
SOCOTEC has performed extensive system and component aging and life cycle management evaluations. These have ranged from procedures for inspection or system walk-downs to prediction of failure probability to the end of plant operation.
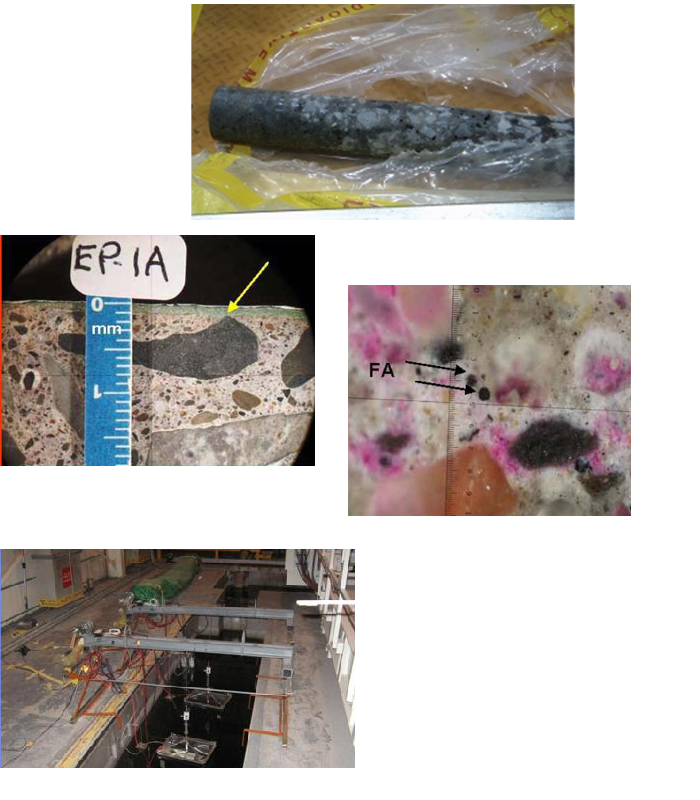
Want to know more about our Nuclear services?
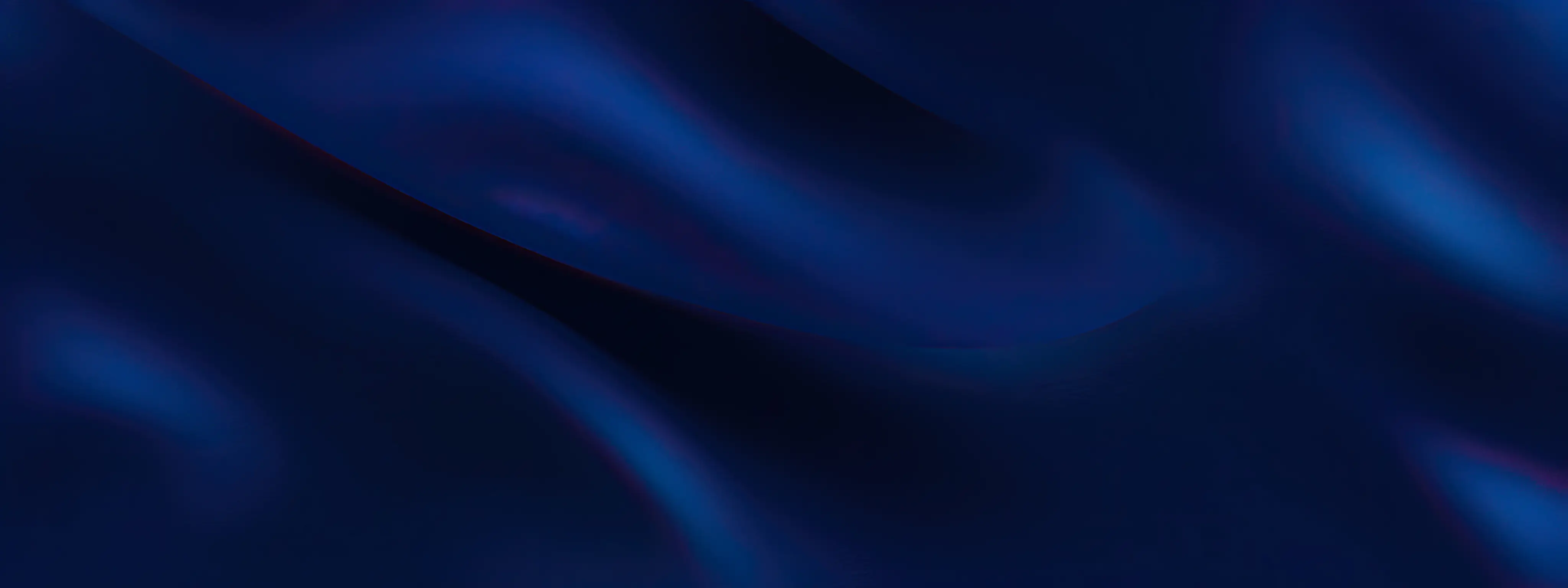